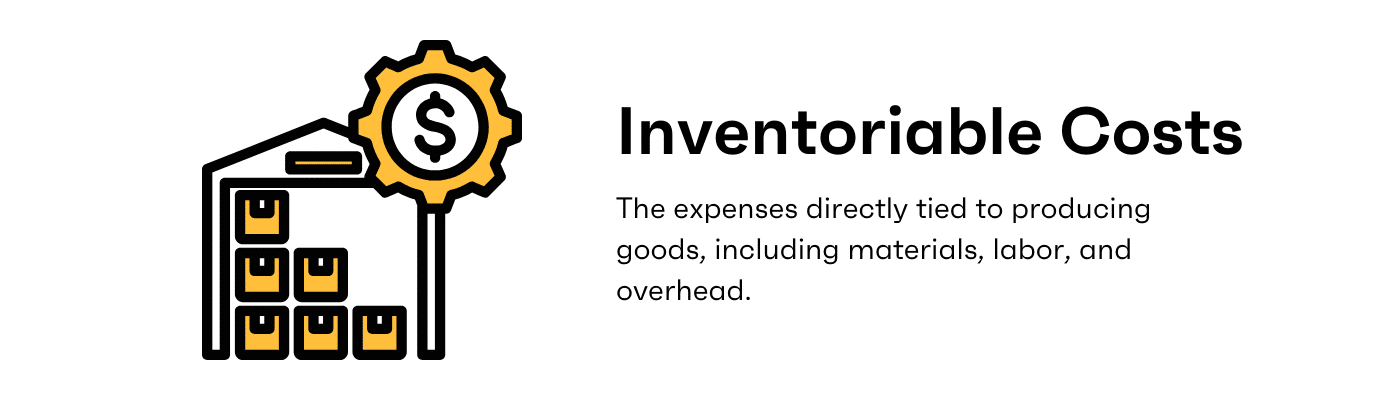
Have you ever wondered how businesses accurately determine the cost of the products they sell? Understanding inventoriable costs is key to unraveling this mystery. Inventoriable costs, also known as product costs, are the expenses directly tied to the production of goods. They include everything from the raw materials used in manufacturing to the wages of the workers who assemble the products. Essentially, they encompass all the costs incurred in turning raw materials into finished goods ready for sale.
In this guide, we’ll explore every aspect of inventoriable costs, from their definition and importance in business operations to the various methods used to calculate and manage them. Whether you’re a business owner, accountant, or simply curious about how businesses operate, understanding inventoriable costs is essential for gaining insight into the financial workings of businesses and making informed decisions about pricing, production, and profitability.
What is Inventoriable Costs?
Inventoriable costs, also known as product costs, are expenses directly associated with the production of goods. These costs are capitalized as inventory on the balance sheet until the goods are sold, at which point they are expensed as cost of goods sold (COGS). Inventoriable costs include direct materials, direct labor, and manufacturing overhead.
Inventoriable costs play a crucial role in determining the true cost of goods sold and the value of ending inventory. Properly managing and tracking inventoriable costs ensures accurate financial reporting, compliance with accounting standards, and informed decision-making regarding pricing strategies, inventory levels, and profitability.
Importance of Inventoriable Costs in Business Operations
The importance of inventoriable costs in business operations cannot be overstated. Effective management of these costs is essential for various aspects of business success:
- Cost Control: Properly managing inventoriable costs helps businesses control expenses associated with production, ensuring cost efficiency and profitability.
- Inventory Valuation: Accurately valuing inventory allows businesses to determine the cost of goods sold (COGS) and the value of ending inventory, providing insights into financial performance and profitability.
- Financial Reporting: Inventoriable costs impact financial statements, including the balance sheet and income statement, ensuring compliance with accounting standards and providing stakeholders with reliable financial information.
- Decision-Making: Understanding inventoriable costs enables businesses to make informed decisions regarding pricing strategies, product profitability analysis, inventory management, and strategic planning.
- Competitive Advantage: Properly managing inventoriable costs provides businesses with a competitive advantage by optimizing production processes, controlling costs, and enhancing profitability.
In summary, inventoriable costs are integral to business operations, financial reporting, and decision-making processes. By effectively managing these costs, businesses can improve cost efficiency, maximize profitability, and achieve long-term success in today’s competitive marketplace.
Types of Inventoriable Costs
In the realm of inventoriable costs, businesses typically categorize them into three main types: direct materials, direct labor, and manufacturing overhead. Each type plays a distinct role in the production process and contributes to the overall cost of goods sold.
Direct Materials
Direct materials are the tangible components or raw materials that are directly incorporated into the production of a finished product. These materials are easily identifiable and can be directly traced to the final product. Examples of direct materials include wood, metal, plastic, fabric, and electronic components.
The cost of direct materials can be calculated using the formula:
Cost of Direct Materials = Beginning Inventory of Raw Materials + Purchases of Raw Materials - Ending Inventory of Raw Materials
This formula takes into account the raw materials inventory at the beginning of a period, any additional materials purchased during the period, and the remaining inventory at the end of the period.
Direct materials are a fundamental component of manufacturing processes across various industries. The cost of direct materials directly impacts the cost of goods sold and the profitability of a product. Therefore, it’s crucial for businesses to accurately track and manage their direct material costs to ensure cost efficiency and competitive pricing.
In addition to the cost of acquiring direct materials, businesses must also consider the cost of storing and handling these materials. Inventory carrying costs, such as storage space, insurance, and handling expenses, contribute to the overall cost of direct materials and should be factored into inventory management strategies.
Direct Labor
Direct labor refers to the wages and benefits paid to employees who are directly involved in the production process. These employees are responsible for physically assembling or manufacturing the goods and directly contribute to the creation of the final product.
The cost of direct labor can be calculated by multiplying the hourly wage rate of each employee by the number of hours worked on the production line.
Direct Labor Cost = Hourly Wage Rate × Number of Hours Worked
Factors such as wage rates, labor hours, and productivity levels influence the cost of direct labor. Businesses must accurately track and allocate direct labor costs to specific products or production batches to determine the true cost of goods sold.
In addition to wages, direct labor costs may also include employee benefits, such as health insurance, retirement contributions, and paid time off. These indirect labor expenses should be considered when calculating the total cost of direct labor.
Manufacturing Overhead
Manufacturing overhead encompasses all indirect costs associated with the production process that cannot be directly attributed to specific units of production. These costs include expenses such as factory utilities, depreciation of equipment, maintenance and repairs, indirect labor, and factory rent.
The allocation of manufacturing overhead costs to units of production is typically done using predetermined overhead rates based on factors such as machine hours, direct labor hours, or production volume.
Managing manufacturing overhead costs is essential for maintaining cost efficiency and profitability in manufacturing operations. By optimizing resource utilization, minimizing waste, and implementing cost-saving measures, businesses can reduce manufacturing overhead expenses and improve overall operational efficiency.
Understanding Direct Materials
Direct materials are the backbone of any manufacturing process, representing the tangible components or raw materials that directly contribute to the creation of a finished product.
What are Direct Materials?
Direct materials encompass any physical components or raw materials that are directly incorporated into the production process to create a finished product. These materials can be easily identified and directly traced to the final product. Examples of direct materials vary depending on the industry but may include:
- Raw metals or alloys used in manufacturing machinery
- Timber or lumber for construction purposes
- Plastic pellets for injection molding
- Electronic components for circuit board assembly
- Fabric and textiles for garment production
Understanding the specific direct materials required for each product is essential for accurate inventory management and cost control.
Cost Determination and Measurement
Determining the cost of direct materials involves tracking and calculating the expenses associated with acquiring and using these materials in the production process. The cost of direct materials can be calculated using the following formula:
Cost of Direct Materials = Beginning Inventory of Raw Materials + Purchases of Raw Materials - Ending Inventory of Raw Materials
This formula accounts for the raw materials inventory available at the beginning of a period, any additional materials purchased during the period, and the remaining inventory at the end of the period. By accurately measuring the cost of direct materials, businesses can determine the true cost of goods sold and make informed pricing decisions.
Importance in Inventory Valuation
Direct materials play a pivotal role in inventory valuation, as they directly contribute to the cost of goods sold (COGS) and the overall valuation of inventory on the balance sheet. Properly valuing inventory ensures accurate financial reporting and provides insights into a company’s profitability and financial health.
Effective management of direct materials is essential for controlling costs, optimizing production processes, and maintaining competitive pricing. By accurately tracking and managing direct material costs, businesses can improve cost efficiency, streamline operations, and enhance profitability. Additionally, understanding the significance of direct materials in inventory valuation helps businesses make informed decisions regarding inventory levels, purchasing strategies, and pricing strategies.
Exploring Direct Labor Costs
Direct labor costs are a fundamental aspect of production, representing the wages and benefits paid to employees directly involved in manufacturing processes.
What are Direct Labor Costs?
Direct labor costs encompass the compensation paid to employees who are directly engaged in the manufacturing or production process. These employees directly contribute to the creation of goods and play a hands-on role in assembling or manufacturing products.
Characteristics of direct labor costs include:
- Direct Involvement: Employees involved in direct labor tasks are directly engaged in the production process, performing activities such as assembly, fabrication, or machining.
- Variable Nature: Direct labor costs often vary with production levels, as increased production typically requires additional labor hours to meet demand.
- Product-Specific: Direct labor costs can be attributed to specific products or production batches, making them an essential component of calculating the cost of goods sold (COGS).
Calculation Methods
Calculating direct labor costs involves determining the total wages and benefits paid to employees directly engaged in production activities. The most common method for calculating direct labor costs is by multiplying the hourly wage rate of each employee by the number of hours worked on the production line.
Direct Labor Cost = Hourly Wage Rate × Number of Hours Worked
Additional factors to consider when calculating direct labor costs include overtime pay, shift differentials, and any applicable fringe benefits such as health insurance or retirement contributions.
Impact on Inventory Valuation
Direct labor costs directly impact inventory valuation and the cost of goods sold (COGS) reported on the income statement. As direct labor costs are incurred during the production process, they are included in the total manufacturing costs of goods produced.
Accurately tracking and allocating direct labor costs to specific products or production batches is essential for determining the true cost of goods sold and maintaining accurate inventory valuation. Properly valuing inventory ensures compliance with accounting standards and provides insights into a company’s profitability and financial performance.
Effective management of direct labor costs involves optimizing labor efficiency, minimizing overtime expenses, and ensuring proper staffing levels to meet production demands. By controlling direct labor costs, businesses can improve cost efficiency, enhance profitability, and maintain competitiveness in the market.
Analyzing Manufacturing Overhead
Manufacturing overhead is a crucial aspect of production costs, encompassing various indirect expenses associated with the manufacturing process.
What is Manufacturing Overhead?
Manufacturing overhead consists of all indirect costs incurred during the production process that cannot be directly attributed to specific units of production. These costs are essential for maintaining production operations but are not directly tied to the creation of individual products. Components of manufacturing overhead may include:
- Factory Utilities: Expenses related to electricity, water, and gas used in the manufacturing facility.
- Depreciation of Equipment: Allocation of the cost of machinery and equipment used in production over their useful life.
- Maintenance and Repairs: Costs associated with maintaining and repairing production machinery and equipment.
- Indirect Labor: Wages and benefits paid to employees indirectly involved in the production process, such as supervisors, maintenance staff, and quality control personnel.
- Factory Rent: Rental expenses for the manufacturing facility or production space.
Understanding the components of manufacturing overhead is essential for accurately allocating these costs to units of production and determining the true cost of goods sold.
Allocation Methods
Allocating manufacturing overhead costs to units of production requires the use of allocation methods to distribute these indirect expenses fairly. Common allocation methods include:
- Predetermined Overhead Rates: Calculating a predetermined overhead rate based on estimated overhead costs and a chosen allocation base, such as machine hours, direct labor hours, or production volume. This rate is then applied to actual production activity to allocate overhead costs.
- Activity-Based Costing (ABC): Assigning overhead costs to specific activities or cost drivers that directly contribute to the incurrence of overhead expenses. This method provides a more accurate allocation of overhead costs based on the activities that drive those costs.
Selecting the most appropriate allocation method depends on factors such as the nature of the production process, the availability of cost data, and the desired level of accuracy in cost allocation.
Significance in Inventory Costing
Manufacturing overhead plays a significant role in inventory costing and the determination of the cost of goods sold (COGS). Properly allocating manufacturing overhead costs to units of production ensures that the cost of goods sold accurately reflects the total cost of producing goods.
Accurate inventory costing is essential for financial reporting purposes, as it impacts the valuation of inventory on the balance sheet and the calculation of gross profit on the income statement. By properly valuing inventory, businesses can make informed decisions regarding pricing strategies, inventory management, and overall profitability.
Effective management of manufacturing overhead costs involves optimizing resource utilization, minimizing waste, and implementing cost-saving measures to improve cost efficiency and profitability in manufacturing operations. By understanding the significance of manufacturing overhead in inventory costing, businesses can enhance their financial performance and competitiveness in the market.
Inventoriable Costs vs. Period Costs
Understanding the distinction between inventoriable costs and period costs is essential for effective cost management and financial reporting.
Differentiation and Comparison
Inventoriable costs, also known as product costs, are expenses directly associated with the production of goods and are capitalized as inventory on the balance sheet until the goods are sold. Examples of inventoriable costs include direct materials, direct labor, and manufacturing overhead.
Period costs, on the other hand, are expenses that are not directly tied to the production process and are expensed in the period incurred. These costs include selling and administrative expenses, such as advertising, salaries of non-production employees, and office rent.
The key differences between inventoriable costs and period costs include:
- Timing of Recognition: Inventoriable costs are recognized as assets on the balance sheet until the goods are sold, whereas period costs are expensed immediately in the period incurred.
- Association with Production: Inventoriable costs are directly associated with the production of goods, while period costs are associated with the overall operation of the business.
Impact on Financial Reporting
The classification of costs as inventoriable costs or period costs has a significant impact on financial reporting:
- Balance Sheet: Inventoriable costs are capitalized as inventory on the balance sheet until the goods are sold, contributing to the value of inventory assets. Period costs, however, are expensed immediately and do not appear on the balance sheet.
- Income Statement: Inventoriable costs are gradually expensed as cost of goods sold (COGS) when the goods are sold, reducing gross profit. Period costs are expensed in the period incurred and appear as selling, general, and administrative expenses on the income statement, impacting net income.
Decision-Making Implications
The classification of costs as inventoriable costs or period costs can influence decision-making in several ways:
- Pricing Decisions: Understanding the cost structure of inventoriable costs can help businesses set appropriate pricing strategies to ensure profitability.
- Product Profitability Analysis: Properly allocating inventoriable costs to products allows businesses to analyze the profitability of individual products and make informed decisions regarding product lines or offerings.
- Inventory Management: Managing inventoriable costs effectively is essential for optimizing inventory levels, minimizing carrying costs, and ensuring efficient use of resources.
By understanding the implications of inventoriable costs and period costs on financial reporting and decision-making, businesses can effectively manage costs, improve profitability, and drive sustainable growth.
Inventory Valuation Methods
Choosing the right inventory valuation method is crucial for accurately determining the cost of goods sold (COGS) and the value of ending inventory. Let’s explore three common inventory valuation methods: FIFO (First In, First Out), LIFO (Last In, First Out), and Weighted Average Cost.
FIFO (First In, First Out)
FIFO is a method of inventory valuation that assumes the first units of inventory purchased or produced are the first to be sold. Under FIFO, the cost of goods sold (COGS) is calculated using the cost of the oldest inventory in stock, while the ending inventory is valued at the cost of the most recently purchased or produced inventory.
FIFO is often preferred in industries where inventory costs tend to increase over time, as it results in a lower cost of goods sold and higher reported profits during periods of rising prices. FIFO closely mirrors the actual flow of goods and is relatively easy to understand and apply.
LIFO (Last In, First Out)
LIFO is a method of inventory valuation that assumes the most recently acquired or produced units of inventory are the first to be sold. Under LIFO, the cost of goods sold (COGS) is calculated using the cost of the newest inventory in stock, while the ending inventory is valued at the cost of the oldest inventory.
LIFO is commonly used in industries where inventory costs tend to decrease over time, as it results in a higher cost of goods sold and lower reported profits during periods of rising prices. LIFO may provide tax advantages by reducing taxable income through higher COGS. However, it may not accurately reflect the actual flow of goods in inventory.
Weighted Average Cost
The weighted average cost method calculates the average cost of inventory by dividing the total cost of goods available for sale by the total number of units available for sale. Under this method, the cost of goods sold (COGS) and ending inventory are valued at the average cost per unit.
The formula for calculating the weighted average cost per unit is:
Weighted Average Cost per Unit = Total Cost of Goods Available for Sale / Total Number of Units Available for Sale
The weighted average cost method smoothens out fluctuations in inventory costs and provides a simple and straightforward approach to inventory valuation. It is often used in industries with relatively stable or fluctuating inventory costs.
Comparison and Selection
Each inventory valuation method has its advantages and implications for financial reporting and tax purposes. The choice of inventory valuation method depends on factors such as industry practices, inventory turnover rates, cost fluctuations, and regulatory requirements.
Before selecting an inventory valuation method, businesses should carefully consider the impact of each method on financial statements, taxable income, and decision-making processes. Consulting with accounting professionals or financial advisors can help businesses make informed decisions regarding inventory valuation methods that align with their business objectives and compliance requirements.
Importance of Proper Inventory Management
Proper inventory management is crucial for businesses of all sizes and industries. It encompasses various processes and strategies aimed at effectively controlling, tracking, and optimizing inventory levels.
- Cost Reduction Strategies: Efficient inventory management helps businesses minimize carrying costs, reduce stockouts, and avoid overstocking, leading to cost savings and improved profitability.
- Optimized Production Processes: By maintaining optimal inventory levels, businesses can streamline production processes, minimize waste, and improve overall operational efficiency.
- Enhanced Customer Satisfaction: Proper inventory management ensures that products are available when customers need them, reducing lead times and enhancing customer satisfaction and loyalty.
- Improved Cash Flow: Effective inventory management helps businesses optimize cash flow by minimizing tied-up capital in excess inventory and reducing the risk of obsolete or slow-moving inventory.
- Accurate Financial Reporting: Properly valuing inventory ensures accurate financial reporting and compliance with accounting standards, providing stakeholders with reliable financial information for decision-making purposes.
- Inventory Turnover Analysis: Monitoring inventory turnover ratios allows businesses to assess inventory performance and identify opportunities for improvement in inventory management practices.
- Supply Chain Optimization: Efficient inventory management is essential for optimizing the entire supply chain, from procurement and production to distribution and fulfillment, leading to improved collaboration and cost savings across the supply chain.
- Regulatory Compliance: Proper inventory management helps businesses comply with regulatory requirements, such as inventory valuation methods and reporting standards, reducing the risk of penalties or fines.
- Risk Mitigation: Effective inventory management helps businesses mitigate risks associated with inventory, such as stockouts, excess inventory, theft, and obsolescence, minimizing potential disruptions to operations and revenue streams.
- Strategic Decision-Making: Accurate and timely inventory data provides valuable insights for strategic decision-making, such as product pricing, promotions, and expansion plans, ensuring alignment with business objectives and market trends.
In summary, proper inventory management is essential for controlling costs, optimizing production, enhancing customer satisfaction, improving cash flow, and supporting strategic decision-making. By implementing effective inventory management practices, businesses can gain a competitive edge, maximize profitability, and achieve long-term success in today’s dynamic business environment.
Conclusion
Inventoriable costs are the backbone of any business’s financial management, playing a pivotal role in determining the true cost of goods sold and the overall profitability of the business. By accurately tracking and managing these costs, businesses can make informed decisions about pricing, production, and inventory management, ultimately driving efficiency and maximizing profitability. Whether it’s understanding the difference between direct materials and manufacturing overhead or selecting the most appropriate inventory valuation method, mastering the concept of inventoriable costs is essential for success in today’s competitive marketplace.
Incorporating effective inventory management practices and properly valuing inventory ensures compliance with accounting standards, provides stakeholders with reliable financial information, and supports strategic decision-making. By recognizing the importance of inventoriable costs and implementing sound inventory management strategies, businesses can gain a competitive edge, improve financial performance, and achieve long-term success in today’s dynamic business environment. So, whether you’re a business owner, accountant, or aspiring entrepreneur, understanding and managing inventoriable costs is key to unlocking the full potential of your business operations.
Get Started With a Prebuilt Template!
Looking to streamline your business financial modeling process with a prebuilt customizable template? Say goodbye to the hassle of building a financial model from scratch and get started right away with one of our premium templates.
- Save time with no need to create a financial model from scratch.
- Reduce errors with prebuilt formulas and calculations.
- Customize to your needs by adding/deleting sections and adjusting formulas.
- Automatically calculate key metrics for valuable insights.
- Make informed decisions about your strategy and goals with a clear picture of your business performance and financial health.